
- This event has passed.
This Seminar is currently Postponed. MSE Seminar: “Tuning Nanostructured Materials for Combustion Applications”
March 21, 2024 at 12:00 AM
Metals powders like aluminum and boron are attractive potential fuel additives for pyrotechnics, propellants and explosives due to their high energy release upon oxidation. However, they tend to agglomerate, have lengthy ignition delays, and low combustion rates/efficiencies. This work aims to design metal powders with tuned surface, micro-structure, morphology, or chemistries to mitigate these challenges and favor the formation of desired products and high energy release; without jeopardizing thermochemical performance, safety, and stability. One approach used is to incorporate elements (like Fe) that can act as oxygen shuttle catalysts for surface reactions or to introduce elements to form exothermic intermetallic products (like Zr). Ball-milling allows a simple one pot technique to incorporate these elements to form metastable nanocomposite powders with lower ignition thresholds and improved combustion efficiencies. Novel experimental and diagnostic tools like x-ray phase contrast imaging (XPCI) and snapshot hyper-spectral imager for emissions and reactions (SHEAR) have been coupled to capture condensed phase/internal particle features and external optical emissions, temperatures, and gas phase species from combustion reactions, respectively. Machine learning is also used to obtain quantitative data: identify trends, detect anomalies, and classify particle events from the videos produced of combustion scenes. Results show that surface modification to boron reduces ignition delays and doping boron with as low as 1wt% Fe improves surface reaction rates in air. Other additives like Bi and Co also help to change boron’s oxidation mechanism. For aluminum, powders can be modified by emulsion assisted milling to produce spheres of various sizes by changing the milling parameter space with process control agents like acetonitrile and hexane, and the addition of Zr can accelerate combustion in thermite formulations and allow Al powders to burn in multiple phases with improved combustion efficiencies.
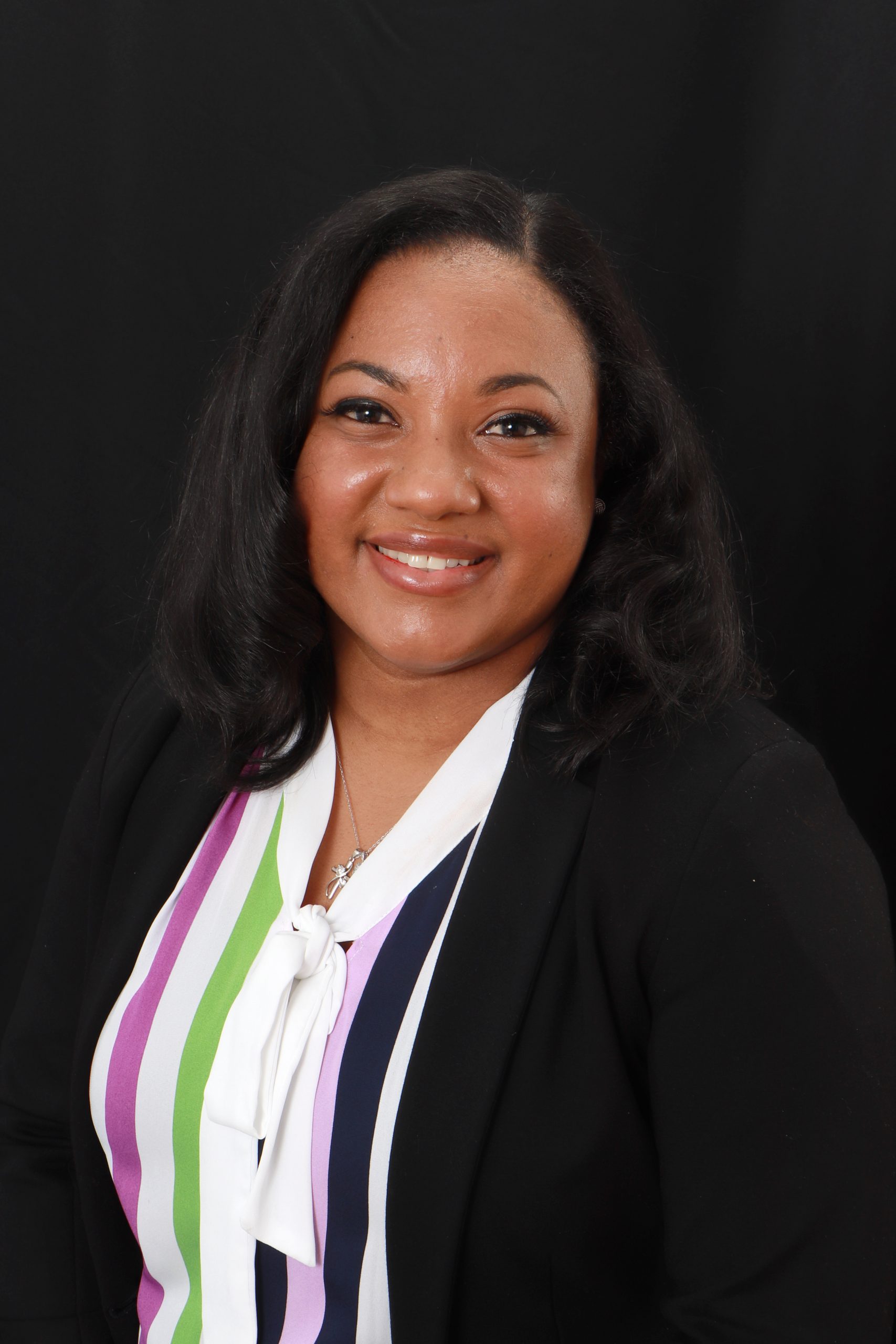
Kerri Lee Chintersingh
Assistant Professor within the Otto H. York Department of Chemical and Materials Engineering at the New Jersey Institute of Technology
Kerri-Lee Chintersingh is an Assistant Professor within the Otto H. York Department of Chemical and Materials Engineering at the New Jersey Institute of Technology. After completing her doctoral degree in Chemical Engineering at NJIT, Dr. Chintersingh joined the Hopkins Extreme Materials Institute and Department of Materials Science and Engineering at the Johns Hopkins University (JHU) as a Postdoctoral Research Fellow in the Weihs group. She is chemical engineering undergraduate alum of the University of Technology, Jamaica, and has served as Process Control Engineer at an alumina refinery.
Currently, her research focuses on tuning nanostructured metals, alloys and composites as powders, or varied architecture for combustion, environment, and energy applications. She is also interested in utilizing machine learning to extract data from complex and extreme environments and to optimize reaction processes and material design. This effort has led to several peer- reviewed publications and multiple research awards. Outside of research, Dr. Chintersingh is a member of the Diversity, Equity and Inclusion Committee within her department and participates in outreach activities to stimulate STEM-based careers, particularly in middle and high school girls. She is also a member of the Society of Women Engineers and the American Institute of Chemical Engineers.